Projects
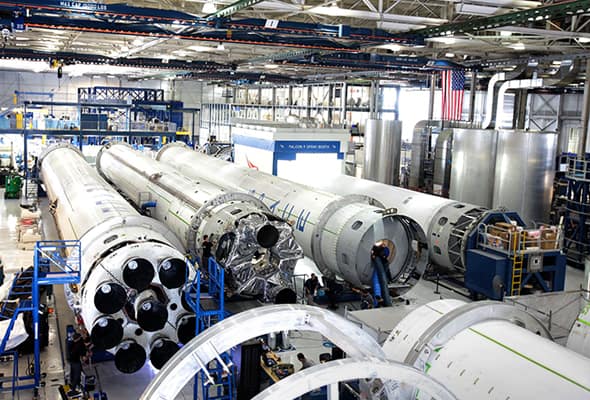
Inductive / Capacitive Sensors
ASTM A848 – 01(2011)
Standard Specification for Low-Carbon Magnetic Iron
Significance and Use
This specification covers the standard requirements for wrought low-carbon iron having a carbon content of 0.015% or less with the remainder of the analysis being substantially iron. These alloys are not electrical steels such as are described in Specifications A 726 and A 840 but are instead primarily used in dc magnetic applications and are produced in a wide variety of mill forms such as forging billet and cold finished bar and wire as well as strip. Two alloy types are covered: Type 1 is a low-phosphorus grade and Type 2 contains a phosphorus addition to improve machinability. Apart from chemical requirements, alloy produced to this specification must exhibit guaranteed maximum values of coercive field strength when heat treated according to this specification. This specification has several useful appendices dealing with typical magnetic, physical and mechanical properties, heat treatment and magnetic aging.
Scope
This specification covers the requirements for wrought low-carbon iron having a carbon content of 0.015 % or less with the remainder of the analysis being substantially iron.
Two alloy types are covered: Type 1 is a low-phosphorous grade and Type 2 contains a phosphorous addition to improve machinability.
This specification also covers alloys supplied by a producer or converter in the form and condition suitable for fabrication into parts which will be subsequently heat treated to create the desired magnetic characteristics. It covers alloys supplied in the form of forging billets, hot-rolled products, and cold-finished bar, wire, and strip.
This specification does not cover iron powders capable of being processed into magnetic components.
This specification does not cover flat-rolled, low-carbon electrical steels.
The values stated in customary (cgs-emu and inch-pound) units are to be regarded as standard. The values given in parentheses are mathematical conversions to SI units which are provided for information only and are not considered standard.
SUY-1 is a soft steel with ultra-low carbon and low impurities.
The grade is defined in the standard, “JIS C 2504 Soft Magnetic Iron,” and is generally referred to as “pure iron.”
There are four SUY grades from SUY-0 to SUY-3. The suffix indicates the material’s magnetic properties with grade 0 providing the best magnetic properties.
Tokkin can manufacture SUY-1.
What is the difference between SUYP and SUYB?
SUY is the general name for this steel grade.
The suffixes P (plate) and B (bar) can be used to identify the shape of the product.
Features
SUY-1 has less carbon content and lower impurities than carbon steel. It also features good drawability and good properties as a soft magnetic material. SUY-1 is mainly used in motor applications, but is recently being used more and more as magnetic shielding.
It has high flux density and coercive force, and these magnetic properties can be maximized if the material is re-subjected to magnetic annealing after the cold-rolling process.
ROLEX METAL DISTRIBUTORS 57-A Khatargalli Thakurdwar Mumbai - 400 002 India 0091-22-23858802 0091-22-23823963 marketing@rolexmetals.com www.rolexmetals.com
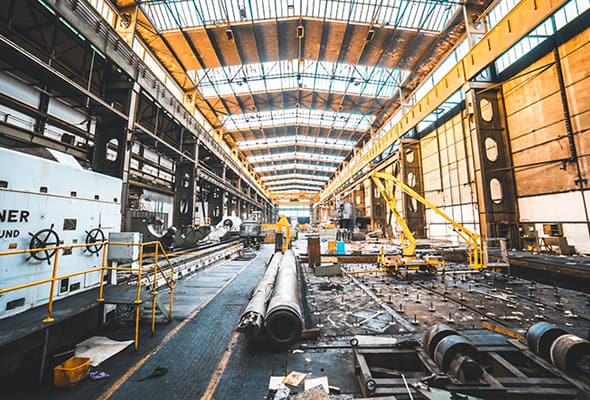
Engineering Class Chains
Electromagnetic pure iron is a type of high quality steel containing over 99.5% of iron with quite low
content of remained elements and featuring with soft texture, strong toughness, easy process and
high electromagnetic performance. Based on its magnetic property, the electromagnetic pure iron
can be classified into three grades: DT4A, DT4E and DT4C. Based on various applications, the
electromagnetic pure iron can be classified into iron core purpose, soft magnetic purpose,
electronic lock purpose, space instruments and military purpose, electron tube purpose and
easy turning electrical purpose.
Electromagnetic pure iron was applied to not only the cutting-edge engineering of national defense
work, but also industrial fields such as relays, instruments and direct current motors. wire and rod
products were mainly used to the civil industry, take the absolute advantage at middle and high-end
and keep growing stably. In recent years, depending on the customer’s requirements, newly
developed ultra-low coercive force electromagnetic pure iron featuring more stable magnetism,
better processing property and lower cost which has been widely used to work and life necessities
in the fields of medical imaging, superconducting power generation and strong/weak magnetic field
shielding of the communication devices.
High-purity iron with purity of 99.987 wt.% was prepared employing a process of direct reduction–melting
separation–slag refining. The iron ore after pelletizing and roasting was reduced by hydrogen to obtain
direct reduced iron (DRI). Carbon and sulfur were removed in this step and other impurities such as
silicon, manganese, titanium and aluminum were excluded from metallic iron. Dephosphorization was
implemented simultaneously during the melting separation step by making use of the ferrous oxide (FeO)
contained in DRI. The problem of deoxidization for pure iron was solved, and the oxygen content of pure
iron was reduced to 10 ppm by refining with a high basicity slag. Compared with electrolytic iron, the pure
iron prepared by this method has tremendous advantages in cost and scale and has more outstanding
quality than technically pure iron, making it possible to produce high-purity iron in a short-flow, large-scale,
low-cost and environmentally friendly way.
We can produce the special type which you ask Applications High purity iron is used largely as the basic
material for (re-)melting of low-carbon, Stainless and acid-resistant steels, materials with a high nickel content,
magnetic alloys as well as stainless and heat resistant steel castings in induction and vacuum furnaces. High
purity iron is also used in many applications of aviation construction, nuclear Technology, the production of
magnets (pole cores, yokes and armatures), in automotive construction, as magnetic shielding, as welding
rods and fuse wire, as gasket in the chemical and petrochemical industry, power station construction, as
anti-corrosion anode and as galvanizing tank including equipment. Mechanical properties Brinell hardness (hb)
High purity iron Max. Typical Cold-rolled strip / sheet 105 90 Hot-rolled strip / plate 105 90 Quarto plate 100 90
Round bar 110 95 Electrical and magnetic properties Characteristics typical values Initial permeability 300 – 500
Permeability 3500 – 6000 Coercive force 60 – 120 a/m Saturation induction 2.15 t Density at 20 °c 7.86 kg/dm³
Melting point 1536 °c Linear expansion coefficient Temperature range 0 – 100 °c 12×10-6 1/°c Modulus of
elasticity 207 kn/mm²
Pure iron, which refers to iron with very few impurities, has excellent properties such as low coercivity,
high ductility, soft texture as well as good performance in thermal conductivity and electrical conductivity.
High-purity iron is widely used in aerospace, radio engineering, the atomic industry and other fields.
It is an important raw material for the production of precision alloys, superalloys, advanced heat-resistant
alloys, amorphous alloys, soft magnetic materials, permanent magnet alloys and other materials. In recent
years, pure iron has been paid more and more attention due to its extensive use and high added-value.
Pure iron is generally categorized as electrolytic iron and technically pure iron. Electrolytic iron can be
prepared by electrolytic refining of high purity ferrous salt solution obtained by ion exchange or solvent
extraction. The purity of a conventional electrolytic iron is about 99.9 wt.%, containing gaseous impurities
such as carbon, nitrogen, oxygen, hydrogen, sulfur and chlorine of more than 500 mass ppm in total.
To obtain higher-purity products, zone refining, electromagnetic levitation melting and vacuum induction
melting are used to further purify electrolytic iron. Since a single purification method cannot meet the
requirements of preparing ultra-high-purity iron, it is necessary to combine various purification methods.
The common process is ion exchange + solvent extraction → electrolytic refining → cold-crucible
melting → zone refining. Many efforts have been devoted to the preparation of high-purity iron.
succeeded in making ultra-high-purity iron of 99.999 wt.% from pure iron by electron beam zone refining
in an atmosphere of ultra-high vacuum. et al. [3–5] made a 7.5 kg ultra-high-purity iron ingot by
careful refining of high purity electrolytic iron. The purity of the purified iron was determined to be
99.9988 wt.% by chemical analysis of 33 elements. et al. [6] developed a process consisting of anion
exchange in a HCl solution, hydrogen reduction and plasma arc melting for the production of semiconductor
grade high-purity Fe with 99.998 wt.% purity. After improving the refining efficiency, the purity of Fe
achieved 99.9993 wt.%
At present, the pure iron that has been produced and applied industrially is called technically pure iron,
with purity ranging from 99.6% to 99.8%. As a raw material for smelting various special alloys such as
superalloys, heat-resistant alloys, precision alloys and maraging steel, technically pure iron has been
widely used in metallurgical industry. Technically pure iron is produced by pyrometallurgy. Firstly, iron
ore is reduced to pig iron in a blast furnace, then excessive carbon is removed by the basic oxygen
furnace (BOF) or electric arc furnace (EAF), and impurities are further eliminated via a secondary refining
route, through which the required purity level is achieved.
During the past few years, the demands for high-quality materials have grown more and more. Some alloys
(e.g., heat-resistant alloys) use technically pure iron in smelting raw materials, but the impurities such as
oxygen, phosphorus and sulfur in technically pure iron are not invariably low. These impurities cannot be
eliminated readily during the alloy smelting process, leading to the situation that the alloy cannot achieve the
desired performance [8]. The quality improvement of technically pure iron produced by hot metal from a
blast furnace is hindered by impurity elements. Besides removing the impurities such as silicon, manganese
and phosphorus, oxygen is injected to remove excess carbon in hot metal. Blowing oxygen causes an
excess of oxygen to be brought into the hot metal, after which it is necessary to add aluminum or strictly
control the C–O reaction using a vacuum for further deoxidation. This lengthy and complicated process,
which revolves around decarbonization and deoxidation, violates the original intention of purification and
makes it difficult to produce pure iron with high cleanliness. On the other hand, the concentrations of gas
impurities (C+N+H+O+S) in common commercial electrolytic iron are generally high. Further refining would
increase the cost and make it difficult to achieve an efficient production. The high-purity iron or ultra-high-purity
iron with 99.99–99.999% purity is too expensive ($7000–200,000 US dollars/tonne) to be used on a large scale.
Research and development of high-purity iron is still in the small-scale laboratory stage, and the supply cannot
meet the demand. Therefore, the manufacture of pure iron has great market potential and profit margin.
How to use short-process, low-cost and environmentally friendly manufacturing technology to produce
high-quality pure iron is the future direction of research.
In this study, an approach of producing high-purity iron is proposed via a direct reduction of iron ore–melting
separation–refining process, by which high-purity iron with purity up to 99.987% can be produced on a large
scale with low cost. The process mainly includes three major steps: Step 1, the iron ore after pelletizing and
roasting is reduced by hydrogen, and direct reduced iron (DRI) that is carbon-free is obtained. Some impurities
such as carbon, sulfur, silicon, manganese, titanium and aluminum cannot be reduced or get into iron in this
step. Step 2, the direct reduced iron is separated into gangue (slag) and metal by melting. In this step, the
composition of slag is adjusted to dephosphorize, if necessary. Step 3, the high basicity slag is dosed to
refining for deoxidation. Similar to the process investigated in this study, researchers have studied the process
of smelting pure iron with DRI in an induction furnace, which has delivered good results. However, these results
still have the capacity to improve the impurities removal in pure iron, especially in solving the problem of
deoxidation of pure iron, so the purity has not reached a high grade. As a comparison, the chemical compositions
of pure iron in this work, typical technically pure iron and typical commercial electrolytic iron, are shown in Table 1.
The purity of pure iron produced by the process has exceeded that of commercial electrolytic iron and technically
pure iron. When the purity of pure iron reaches 3N level or above, it is very difficult to further improve the purity,
and the increase of cost and price brought by this is an exponential growth. The pure iron obtained by this method
has tremendous advantages in cost and scale compared with electrolytic iron and has more outstanding quality
than technically pure iron. This is because this process takes full advantage of the purity advantage of DRI and
solves the problem of deoxidization of pure iron in the context of large-scale production. This paper mainly
expounds upon the experimental process and related mechanism of producing high-purity iron by this method,
as well as the feasibility of industrialization.
Table 1. The chemical compositions of pure iron in this work, typical technically pure iron and typical commercial electrolytic iron (wt.%).
Element Pure Iron in This Work Typical Technically Pure Iron Typical Commercial Electrolytic Iron
C 0.0024 0.0030 0.0057
Si 0.0011 0.0100 0.0030
Mn 0.0003 0.0400 0.0003
P 0.0018 0.0021 0.0005
S 0.0005 0.0016 0.0018
Cr 0.0009 0.0100 0.0003
Ni 0.0005 0.0100 0.0032
Al 0.0015 0.0150 0.0011
Ti 0.0003 0.0011 0.0009
Cu 0.0001 0.0100 0.0015
Mo 0.0007 0.0020 0.0004
V 0.0005 0.0020 0.0003
N 0.0015 0.0025 0.0038
H 0.0001 0.0001 0.0013
O 0.0010 0.0030 0.0574
Purity of Fe 99.9868 99.8876 99.9185
ROLEX METAL DISTRIBUTORS 57-A Khatargalli Thakurdwar Mumbai - 400 002 India 0091-22-23858802 0091-22-23823963 marketing@rolexmetals.com www.rolexmetals.com

Mounted Ball Bearing Units
GOST 11036-75
Steel Grade11895
11895 steel is used: for magnetic circuits of electrical machines and devices.
Steel hot rolled and forged, undoped silicon with specified ageing coefficient, coercive force in open circuit ≤ 95 A/m.
Steel Grade 21895
21895 steel is used: for magnetic circuits of electrical machines and devices.
Steel grooved, undoped silicon with specified ageing coefficient, coercive force in open circuit ≤ 95 A/m.
Steel Grade 21880
21880 steel is used: for magnetic circuits of electrical machines and devices.
Steel grooved, undoped silicon with specified ageing coefficient, coercive force in open circuit ≤ 80 A/m.
Steel Grade 21860
21860 steel is used: for magnetic circuits of electrical machines and devices.
Steel grooved, undoped silicon with specified ageing coefficient, coercive force in open circuit ≤ 60 A/m.
Steel Grade 21850
21850 steel is used: for magnetic circuits of electrical machines and devices.
Steel grooved, undoped silicon with specified ageing coefficient, coercive force in open circuit ≤ 50 A/m.
Steel Grade 20895
Steel 20895 applied: for magnetic circuits of electrical machines and devices.
Steel grooved, undoped silicon without standardization of ageing coefficient, coercive force in open circuit ≤ 95 A/m.
Steel Grade 20880
Steel 20880 applies: for magnetic circuits of electrical machines and devices.
Steel grooved, undoped silicon without standardization of ageing coefficient, coercive force in open circuit ≤ 80 A/m.
Steel Grade 20860
20860 steel is used: for magnetic circuits of electrical machines and devices.
Steel grooved, undoped silicon without standardization of ageing coefficient, coercive force in open circuit ≤ 60 A/m.
Steel Grade 20850
20850 steel is used: for magnetic circuits of electrical machines and devices.
Steel grooved, undoped silicon without standardization of ageing coefficient, coercive force in open circuit ≤ 50 A/m.
Steel Grade 11880
11880 steel is used: for magnetic circuits of electrical machines and devices.
Steel hot rolled and forged, undoped silicon with specified ageing coefficient, coercive force in open circuit ≤ 80 A/m.
Steel Grade 11860
11860 steel is used: for magnetic circuits of electrical machines and devices.
Steel hot rolled and forged, undoped silicon with specified ageing coefficient, coercive force in open circuit ≤ 60 A/m.
Steel Grade 11850
Steel 11850 applies: for magnetic circuits of electrical machines and devices.
Steel hot rolled and forged, undoped silicon with specified ageing coefficient, coercive force in open circuit ≤ 50 A/m.
Steel Grade 10895
10895 steel is used: for magnetic circuits of electrical machines and devices.
Steel hot rolled and forged, undoped silicon without standardization of ageing coefficient, coercive force in open circuit ≤ 95 A/m.
Steel Grade 10880
10880 steel is used: for magnetic circuits of electrical machines and devices.
Steel hot rolled and forged, undoped silicon without standardization of ageing coefficient, coercive force in open circuit ≤ 80 A/m.
Steel Grade 10864 (03; NJ)
10864 steel is used: for the manufacture of parts of vacuum devices and components of magnetic circuits of electrical machines and devices.
The low carbon steel.
Steel Grade 10860
Steel 10860 applies: for magnetic circuits of electrical machines and devices.
Steel hot rolled and forged, undoped silicon without standardization of ageing coefficient, coercive force in open circuit ≤ 60 A/m.
Steel Grade 10850
Steel 10850 applies: for magnetic circuits of electrical machines and devices.
Steel hot rolled and forged, undoped silicon without standardization of ageing coefficient, coercive force in open circuit ≤ 50 A/m.
ROLEX METAL DISTRIBUTORS 57-A Khatargalli Thakurdwar Mumbai - 400 002 India 0091-22-23858802 0091-22-23823963 marketing@rolexmetals.com www.rolexmetals.com
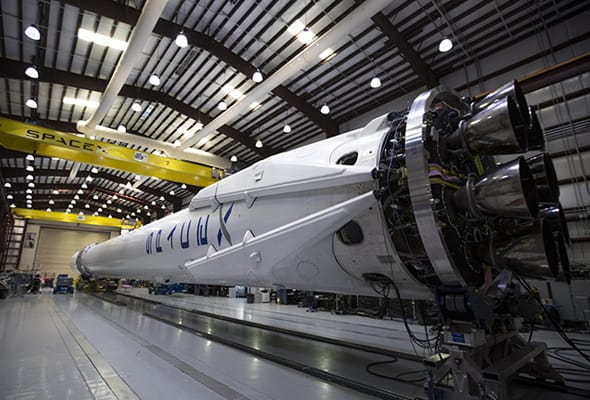
High Quality Gears & Conveyors
SIGNALING RELAYS
We offers a wide range of Q SERIES RAILWAY SIGNALLING RELAYS to meet all types of Signalling
Circuit Applications such as Route Relay Interlocking, Panel Interlocking, Automatic Signalling,
Point Operation and Track Circuiting. Each individual type of relay undergoes extensive TYPE TESTING
by Research Design and Standards Organization (R.D.S.O., Lucknow) of the Indian Railways and
approved for use in Railway signalling circuits.
NEUTRAL LINE RELAYS
This is a DC neutral line relay fitted with independent non-fusible contacts.
It meets the requirements of relevant BRB Spec.
Relay types covered under this category are:
QN1 – Line Relay complying with BRS 930.
QNA1 – AC immune Line Relay complying with BRS 931A.
QS3 & QN1K – Neutral Line sensitive Relay complying with BRS 930
QNN1 – Twin Line Relay complying with BRS 960.
QNNA1 – Twin AC Immune Relay complying with BRS 966 F6.
QNA1K – AC immune, DC neutral, tractive armature, line relay with BRS 931 A.
TRACK RELAYS
These are tractive armature; DC neutral track relays designed for use in DC track Railway Signalling circuits.
The contacts are Silver Impregnated Graphite to Silver.
Relay types covered under this category are:
QT2 – DC Track Relay to BRS 938 A
QTA1 – DC AC Immune Track Relay complying with BRS 939A
QTA2 – DC AC Immune Track Relay complying with BRS 966 F2
QBAT – DC Baised AC Immune Track Relay as per RDSO spec RDSO/SPN/84-88.
BIASED RELAYS
These are miniature AC immune, DC biased; tractive armature line relays designed for Railway Signalling
purposes where the operation of the relay is dependent on the polarity of the coil current in the circuits
and where alternating currents at industrial frequencies (50 Hz) may be present.
Relay types covered under this category are:
QBA1 – DC Biased AC Immune Line Relay complying with BRS 932A
QBBA1 – Twin DC Biased AC Immune Line Relay complying with BRS 961
QBCA1 – DC Biased AC Immune Point Contactor Relay complying with
BRS 943 and 966 F4.
LAMP PROVING
These are AC operated tractive armature miniature relays designed for use in Railway Signalling Lamp
Proving & LED Circuits. The contacts are Silver Impregnated Graphite to Silver. These relays comply
with BRB Specifications 941A and in some special cases governed by Indian Railway requirement.
Individual relays of this style have different characteristics or operating parameters to meet a variety
of lamp proving & LED needs. All relays are slugged to some extent where “Supply Interruption Time”
is guaranteed. The same is mentioned in the detailed specifications.
LATCH RELAYS
These are DC tractive armature magnetically latched line relays, designed for use where a self-latching
relay with a separate release winding is required. The relay is held in full operating condition by a
permanent magnet, releasing only when the release coil is energized. A high back stop pressure
ensures that the armature will not move and latch up accidentally due to vibration. The contacts are
Silver Impregnated Graphite to Silver and the relay complies with BRB Specs. 935 A.
SLOW IN ACTION RELAYS
These are slow operate, AC immune, DC neutral line relays, designed primarily as a track circuit
repeater relay for use in circuits or where release time sufficient to cover the transit time of an
AC immune neutral line relay.
Relay types covered under this category are:
QSPA1 – AC Immune DC neutral line, slow to pick up relays as per BRS 933A.
QSRA1 – AC Immune DC neutral line, slow to release relays as per BRS 934A.
OTHER RELAYS
AC tractive armature line relay to be driven from 110 Volts AC design for interfacing between the
electronic circuitry of “Solid State Interlocking” or ” Computer Based Interlocking ” systems and
other equipments.
Relay types covered under this category are:
QNHX1 – AC tractive, 110V AC relay complying with BRS 966 F7.
QNHXC1 – AC tractive, 110V AC relay complying with BRS 966 F7.
Relays in Railway Signalling
Relay manufacturers for Railway Control System say that the system of relays is used to keep trains
on the right track and conduct traffic. Since trains are heavy, produce immense inertia and run on
fixed tracks the chances of collision increases substantially.
The relays that are used for railway signalling are mostly large considering voltages and currents that
are switched are small. The railway signalling circuits are highly reliable that use special techniques
to detect and prevent failures in the relay system.
There are two main types of relays used for railway signalling:
Track relays – They are connected across the track circuit.
Line relays -The relays that are used for any other purpose except for track are the line relays.
Metal to Metal TM type signalling relays for the Indian Railways with technical specification of RDSO
When an electric current passes through a conductor a magnetic field is produced around the conductor.
This effect can be easily demonstrated by showing that a compass needle is deflected when placed near
a wire carrying an electric current. If the wire is coiled in a spiral, then the magnetic field will be perpendicular
to the direction of the current.
In an electromagnet a wire is wrapped around a soft iron core. When current is passed through the wire the
core carries the magnetic flux and behaves like a bar magnet. This type of magnet has the advantage that
the magnet field can be switched on or off.
A relay is an electromechanical switching device. It has one or more contacts for opening and closing circuits.
A movable metal strip called an armature is activated by an electromagnet. The movement of the armature
causes the contacts to either open or close, thereby turning a circuit on or off. In some designs the armature
is a drum that rotates when the magnetic field is activated.